Top Quality CNC Machining Services for Custom Stainless Steel Parts from China
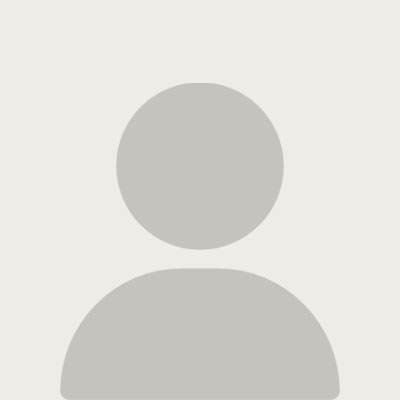
By
Shahbaz Ahmed - July 12, 2024
CNC Machining Services
What Are the Benefits of Using Custom CNC Machining Services in China?
How Does Precision CNC Machining Improve Quality?
Precision CNC machining improves quality by ensuring high levels of accuracy and consistency in the production of parts. This process involves the use of computer-controlled machines that follow precise design specifications, minimizing human error. The result is components with tight tolerances and impeccable surface finishes, which are essential for applications that require exact measurements and high performance. Additionally, the repeatability of CNC machining ensures that each part is identical to the next, reducing variability and enhancing the overall reliability of the final product.
If you are looking for more information about Custom Stainless Steel CNC Machining Services From China go here right away.
What Are the Cost Benefits of CNC Machining Services in China?
- Lower Labor Costs: China offers competitive labor costs compared to many Western countries, allowing for more affordable production without compromising on quality.
- Advanced Technology: Chinese CNC machining facilities often employ the latest technology and equipment, which can enhance production efficiency and reduce overall costs.
- Economies of Scale: Large-scale production capabilities in China mean lower per-unit costs, translating to cost savings for businesses needing bulk orders.
- Material Sourcing: Proximity to various raw material suppliers allows Chinese manufacturers to acquire materials at lower costs, further decreasing the expense of manufacturing.
Why Choose Custom Precision CNC Machining?
- Design Flexibility: Custom machining provides the flexibility to create complex geometries that meet specific project requirements.
- High Precision: Achieve exact specifications and tight tolerances, which are crucial for high-performance applications.
- Scalability: Custom CNC machining can efficiently handle both small and large production runs, adapting to your business needs.
- Quality Assurance: Stringent quality control measures ensure that each part conforms to industry standards and customer specifications.
- Cost Efficiency: Reduces waste and enhances resource utilization, leading to cost-effective production processes.
What Types of Stainless Steel Alloys Are Best for CNC Machining?
Advantages of Using 304 Stainless Steel
- Corrosion Resistance: 304 stainless steel is renowned for its excellent resistance to corrosion, making it ideal for use in a wide range of environments, including those that are moist or acidic.
- Durability: Known for its high tensile strength and toughness, 304 stainless steel provides long-lasting performance in various applications.
- Ease of Fabrication: This alloy can be easily welded, cut, and formed, offering flexibility in manufacturing processes.
- Hygienic Properties: Its smooth surface and resistance to staining make 304 stainless steel a preferred choice in industries where hygiene is paramount, such as food and beverage or healthcare.
Applications of Stainless Steel 316
- Marine Environments: Due to its superior resistance to chlorides and saltwater, stainless steel 316 is extensively used in marine hardware, fasteners, and fittings.
- Chemical Processing: The alloy's corrosion resistance extends to a variety of chemicals, making it suitable for tanks, pipes, and heat exchangers in chemical plants.
- Medical Devices: Its biocompatibility and resistance to sterilizing solutions make 316 stainless steel a favored material for surgical instruments and implants.
- Food and Beverage Industry: 316 stainless steel is often used in the production of food processing equipment, brewery tanks, and kitchen appliances, thanks to its resistance to food acids and cleaning agents.
How Does Using Stainless Steel 303 Affect Machining Processes?
- Enhanced Machinability: Stainless steel 303 contains sulfur, which enhances its machinability, making it easier to cut compared to other stainless steel grades.
- Surface Finish: The sulfur addition may, however, lead to surface defects if not managed properly during the machining process.
- Tool Wear: The improved machinability reduces tool wear and extends the tool life, resulting in cost savings for prolonged production runs.
- Mechanical Properties: While 303 offers good mechanical properties, it is generally softer and may not be as suitable for high-stress applications compared to other stainless steels like 304 or 316.
What Are the CNC Machining Capabilities for Stainless Steel Parts?
What is the Precision Range for CNC Machined Parts?
The precision range for CNC machined parts can vary based on multiple factors, including the machine's capabilities, the material being used, and the specific tolerances required for the part. Generally, CNC machining can achieve tolerances as tight as ± 0.001 inches (± 0.025 mm). This level of precision makes CNC machining highly suitable for applications requiring high accuracy and repeatability.
Which Machine Parts Can Be Custom Made with CNC Milling?
CNC milling is versatile and can be used to custom manufacture a wide range of machine parts, including:
- Engine Components: Custom engine blocks, cylinder heads, and other critical engine parts.
- Aerospace Parts: Structural elements, turbine blades, and complex components for aircraft and spacecraft.
- Medical Devices: Precision surgical instruments, prosthetic limbs, and implants.
- Automotive Parts: Gearboxes, suspension components, and custom body panels.
- Industrial Equipment: Valves, fittings, and specialized machinery components.
What Kind of Surface Finishes Are Available for Stainless Steel Parts?
CNC machined stainless steel parts can be finished with a variety of surface treatments to enhance their appearance, durability, and corrosion resistance:
- Polishing: Achieves a smooth, mirror-like finish.
- Brushing: Provides a uniform, matte texture with fine lines.
- Passivation: Enhances corrosion resistance by removing free iron from the surface.
- Electropolishing: Polishes and deburrs simultaneously, yielding a high-gloss finish.
- Bead Blasting: Imparts a textured, matte surface through the use of fine glass beads.
How Do You Choose the Ideal Supplier of Custom Precision CNC Machining Services?
What Criteria Determine the Best CNC Machining Supplier in China?
Selecting the best CNC machining supplier in China requires careful consideration of several critical factors:
- Experience and Expertise: Suppliers with a proven track record and extensive experience in specific industries.
- Certifications: ISO 9001, AS9100, or other relevant certifications that demonstrate a commitment to quality and industry standards.
- Technological Capabilities: Access to advanced CNC machinery and software that ensures precision and efficiency.
- Quality Control: Robust inspection processes and quality control measures, such as CMM (Coordinate Measuring Machine) and in-process monitoring.
- Customer Support: Responsive and knowledgeable customer service that can provide technical support and address concerns promptly.
- Logistics and Delivery: Reliable and efficient supply chain management that ensures timely delivery of parts.
How to Ensure Quality in Stainless Steel CNC Machining Services?
Ensuring quality in stainless steel CNC machining services involves implementing several best practices:
- Material Selection: Use of high-quality stainless steel alloys suitable for the intended application.
- Tooling and Techniques: Employing the right cutting tools and machining techniques to prevent work hardening and achieve precise tolerances.
- Surface Finishing: Utilizing appropriate surface finishing methods to meet specific aesthetic and functional requirements.
- Inspection Protocols: Conducting thorough inspections at various stages of production to verify dimensions, tolerances, and surface finish.
- Documentation: Maintaining meticulous records of all processes and inspections to ensure traceability and accountability.
What Should You Look for in a Machining Service for Custom Parts?
When choosing a machining service for custom parts, consider the following checklist:
- Capabilities: Ability to handle the complexity and volume of your project.
- Customization: Willingness and ability to provide bespoke solutions tailored to your specifications.
- Quality Assurance: Implementation of stringent quality control measures and inspection processes.
- Lead Time: Capacity to meet your timeframes without compromising on quality.
- Cost-Effectiveness: Competitive pricing without sacrificing the quality of materials and workmanship.
- Customer Reviews and References: Positive feedback and recommendations from previous clients.
- After-Sales Support: Availability of post-delivery support and services, including modifications and troubleshooting.
These criteria will help you identify the most reliable and effective CNC machining services for your specific needs.
How Do CNC Machining Services Handle Complex Stainless Steel Components?
What are the Benefits of Using CNC Turning for Complex Designs?
CNC turning offers numerous advantages when it comes to manufacturing complex designs:
- High Precision: Modern CNC turning machines are capable of achieving extremely tight tolerances, ensuring that even the most intricate designs are manufactured to exact specifications.
- Consistency: The automated nature of CNC turning ensures that each part produced is identical, which is essential for maintaining consistency in complex designs.
- Flexibility: CNC turning can accommodate a wide range of materials and design complexities, making it suitable for both prototype development and large production runs.
- Efficiency: The ability to program complex tool paths and automate the machining process significantly reduces production time and costs.
- Reduced Waste: Precise material removal and optimized tool paths minimize waste, making the process more cost-effective and environmentally friendly.
How Are High Precision Custom Stainless Steel Parts Achieved?
Achieving high precision in custom stainless steel parts involves several critical steps:
- Material Selection: Choosing the appropriate grade of stainless steel based on the required mechanical properties and intended application.
- Tooling Selection: Utilizing high-quality cutting tools and inserts specifically designed for stainless steel machining to ensure optimal performance and longevity.
- Machine Calibration: Regularly calibrating and maintaining CNC machines to ensure they operate within specified tolerances.
- Advanced Programming: Leveraging sophisticated CAD/CAM software to create detailed and accurate machining programs.
- Controlled Environment: Maintaining a stable machining environment with controlled temperature and humidity to prevent material deformation and ensure precision.
What is the Process for Machining Intricate Stainless Steel Components?
The process for machining intricate stainless steel components typically follows these steps:
- Design and Prototyping: Developing detailed CAD models and prototypes to confirm design specifications and feasibility.
- Material Preparation: Selecting and preparing the stainless steel stock material for machining.
- Machine Setup: Configuring the CNC machine with the appropriate tools, fixtures, and programs.
- Rough Machining: Performing rough cutting operations to remove the bulk of the material and create the basic shape.
- Finishing: Conducting finishing operations to achieve the desired surface finish and precise tolerances.
- Quality Control: Inspecting the machined components using advanced metrology equipment to verify dimensions and tolerances.
- Surface Treatment: Applying necessary surface treatments, such as polishing or coating, to enhance the part's functional and aesthetic properties.
- Final Inspection: Conducting a final inspection to ensure all specifications are met before the components are approved for delivery.
Â
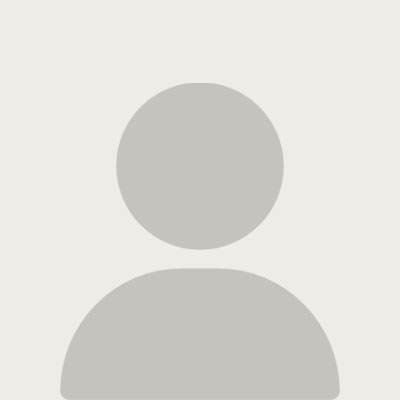
By
Shahbaz Ahmed - July 12, 2024
Leave a comment