Digital Twins in Cable Manufacturing A Game Changer for Precision
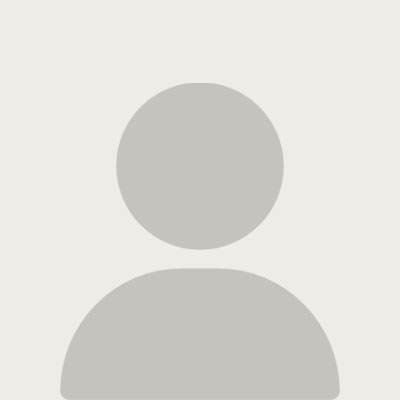
By
Shahbaz Ahmed - February 17, 2025
Pixabay
The cable manufacturing industry is undergoing a digital transformation, with digital twins emerging as a game-changing technology that enhances precision, efficiency, and quality. By creating virtual replicas of physical production processes, manufacturers can simulate, monitor, and optimize operations in real time. This technology enables proactive maintenance, predictive analytics, and automated decision-making, ensuring higher efficiency and reduced downtime.
In an era where Industry 4.0 and smart manufacturing are redefining production landscapes, digital twins offer cable manufacturers a way to reduce waste, improve product quality, and increase operational agility. By bridging the gap between physical and digital systems, digital twins allow manufacturers to visualize and control every aspect of the production lifecycle.
1. What is a Digital Twin in Cable Manufacturing?
A digital twin is a real-time virtual model of a physical asset, process, or system that continuously receives data from sensors, IoT devices, and AI-driven analytics. In cable manufacturing, digital twins replicate the entire production process, from raw material selection to final product testing.
- Real-Time Monitoring: Digital twins track production metrics like tension, insulation thickness, and material consistency.
- Process Simulation: Virtual models simulate how different production parameters affect cable quality and durability.
- Predictive Analytics: AI-driven insights forecast potential failures, allowing preventive maintenance before costly breakdowns occur.
By leveraging digital twin technology, manufacturers gain unparalleled visibility into their production lines, enabling data-driven decision-making and operational optimization.
2. Key Benefits of Digital Twins in Cable Manufacturing
Digital twin technology offers several benefits that enhance precision and efficiency in cable manufacturing:
a) Increased Production Efficiency
- Digital twins provide real-time performance insights, allowing manufacturers to adjust parameters for optimal production speed and material usage.
- Automated adjustments help prevent material waste and energy overconsumption.
b) Predictive Maintenance for Reduced Downtime
- AI-powered monitoring detects early signs of wear and tear in machinery, preventing costly breakdowns.
- Machine learning algorithms predict component failures and suggest maintenance schedules to avoid unexpected stoppages.
c) Quality Control and Product Consistency
- Sensors collect real-time quality data, ensuring that every batch of cable meets stringent industry standards.
- Digital twins enable real-time defect detection, reducing the number of faulty products.
d) Sustainability and Waste Reduction
- Optimized material usage minimizes excess waste.
- Energy-efficient production lowers carbon footprints by optimizing power consumption in manufacturing processes.
e) Faster Time-to-Market
- Virtual simulations enable rapid design iterations without requiring physical prototypes.
- Automated testing speeds up compliance verification, reducing delays in product launches.
3. How Digital Twins Work in Cable Production
The digital twin framework in cable manufacturing consists of three main components:
a) Physical System (Production Line)
The real-world factory floor, including machines, sensors, and robotic systems involved in cable production.
b) Digital Replica (Virtual Model)
A high-fidelity digital model that mirrors the physical system in real time, simulating production parameters, environmental factors, and operational conditions.
c) Data Connectivity (IoT and AI Integration)
Sensors collect data on:
- Material flow (e.g., copper, aluminum, insulation compounds)
- Tension and extrusion pressure
- Temperature and humidity conditions
- Speed and efficiency of cable winding and coating
This data feeds into AI-driven analytics, allowing manufacturers to fine-tune production processes for maximum efficiency and quality.
4. Real-World Applications of Digital Twins in Cable Manufacturing
Several leading cable manufacturers are already implementing digital twin technology to enhance production. Some key applications include:
a) Smart Cable Design and Prototyping
- Virtual modeling of different cable configurations allows rapid testing of new insulation materials, conductor types, and coatings without physical prototypes.
- Simulations predict performance under stress, temperature fluctuations, and mechanical bending, ensuring cables meet industry standards before production begins.
b) Optimizing Extrusion and Insulation Processes
- Digital twins monitor polymer flow dynamics, ensuring precise insulation thickness and uniformity.
- AI-driven controls adjust extruder speed, temperature, and pressure to eliminate waste and defects.
c) Enhancing Energy Efficiency in Manufacturing
- Smart monitoring of power usage identifies inefficiencies in heating elements, motors, and cooling systems.
- AI-driven adjustments reduce energy consumption, supporting sustainable production.
d) Improving Supply Chain Management
- Digital twins optimize inventory tracking and logistics, preventing shortages or overstocking.
- Real-time supplier performance tracking ensures that only high-quality materials enter the production cycle.
5. Challenges in Implementing Digital Twins in Cable Manufacturing
While digital twin technology offers significant advantages, implementation comes with challenges:
a) High Initial Investment
- Deploying IoT sensors, AI software, and cloud computing infrastructure requires upfront capital.
- ROI is typically realized through long-term efficiency gains and reduced operational costs.
b) Data Security and Integration Issues
- Large-scale data collection introduces cybersecurity risks.
- Integrating digital twin systems with legacy manufacturing setups requires robust IT solutions.
c) Workforce Upskilling
- Factory personnel must adapt to new AI-driven monitoring systems.
- Training programs are essential for successful technology adoption.
Despite these challenges, the long-term benefits of precision, cost savings, and efficiency improvements outweigh the initial implementation hurdles.
6. Future Trends: The Evolution of Digital Twins in Manufacturing
The future of digital twins in cable manufacturing includes:
a) AI-Driven Predictive Maintenance
- Advanced machine learning models will improve failure detection and maintenance automation.
b) Integration with 5G and Edge Computing
- Faster data transmission will enhance real-time monitoring.
- Edge computing reduces reliance on cloud-based data storage, improving response times.
c) Blockchain for Supply Chain Transparency
- Digital twin-enabled blockchain tracking ensures that raw materials, production stages, and final products are fully traceable.
d) Self-Healing Manufacturing Systems
- AI-powered automated calibration will allow machines to adjust production parameters autonomously to correct minor defects in real time.
Conclusion:
Digital twins are revolutionizing the cable manufacturing industry by providing unmatched precision, efficiency, and quality control. By simulating, monitoring, and optimizing production processes in real time, manufacturers can reduce costs, minimize waste, and accelerate product development.
Companies like Ducab are embracing Industry 4.0 solutions, leveraging digital twin technology to drive smart manufacturing innovations and enhance operational resilience. As the industry continues to evolve, AI-driven digital twins will play a pivotal role in shaping the future of cable production.
FAQs: Digital Twins in Cable Manufacturing
1. What is a digital twin in cable manufacturing?
A digital twin is a real-time virtual model that replicates the cable production process, using sensor data and AI to optimize efficiency.
2. How do digital twins improve production efficiency?
They monitor real-time performance, enable predictive maintenance, and automate adjustments for optimized material usage.
3. What are the key challenges in implementing digital twins?
High initial investment, data security concerns, and the need for workforce training are common challenges.
4. How do digital twins enhance quality control?
They enable real-time defect detection, ensuring consistent cable dimensions, insulation thickness, and durability.
5. How does Ducab integrate digital twin technology?
Ducab utilizes digital twin solutions to enhance cable precision, sustainability, and smart manufacturing capabilities.
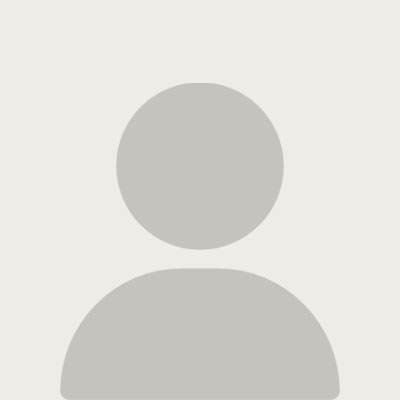
By
Shahbaz Ahmed - February 17, 2025
Leave a comment